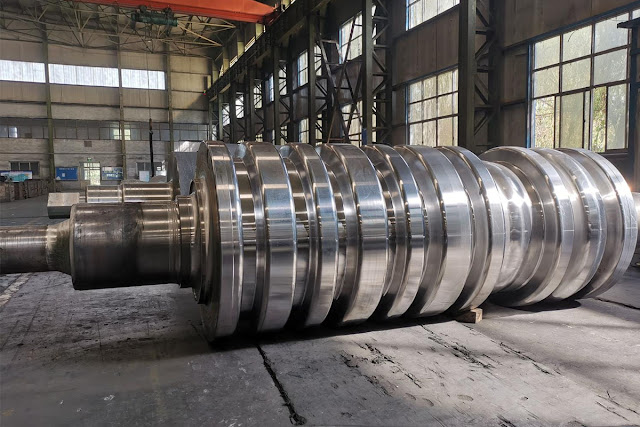
Residual stress and thermal stress will occur in the preparatory process before the roll is manufactured and used. During application, it was further subjected to various periodic stress effects, including tortuosity, change, shear force, contact stress and thermal stress. The distribution of these stresses along the roll body is uneven and constantly changing. The reason is not only the planning factors, but also the continuous changes in the wear, temperature and roll shape of the roll in use. In addition, rolling conditions often exhibit abnormal conditions. Improper cooling of the rollers after application will also be endangered by thermal stress.
Therefore, in addition to wear, the roll often exhibits various partial damages and appearance damages such as cracks, fractures, flaking, and indentation. A good roll should have a better match between its strength, wear-resistance and various other performance indicators. In this way, it is not only durable under normal rolling conditions, but also less damaging when presenting some abnormal rolling conditions. Therefore, when making rolls, the metallurgical quality of the rolls must be strictly controlled or supplemented with external measures to enhance the bearing capacity of the rolls.
Various types of rolling mills produce long products. Therefore, the selection and layout of rolling mill types, the selection of roll materials, and the determination of roll sizes are also very wide. At the same time, the rolls selected by different rolling mills are also different, and the rolls need to be selected according to production requirements.
Before choosing the right roll to increase productivity and improve product quality, you need to fully understand the types and configurations of various mills.
1. Bar and small section rolling mill
Generally speaking, bar and small section rolling mills can use either steel ingots with a size range of 80 to 150 mm or continuous casting billets with the same size range to produce small profile and bars. The initial feed temperature of the bar and small profile rolling mill is 1200°C. The rolling mill can be produced either semi-continuously or fully continuously. Continuous rolling mill is the current development trend, during which there are rough rolling, intermediate rolling and finishing rolling stands. The roughing stands are arranged in horizontal/vertical order, which mainly depends on the product composition. The intermediate stand and the finishing stand can be either vertical or horizontal. For the bar, the rolling mill constitutes more vertical stands, while for other small profiles, the horizontal stand is often used.
In the small profile rolling mill, the diameter of the selected roll is 300-600mm, and the length of the roll body is 700mm according to the difference between the raw materials fed and the final product size. For product tolerances, users generally require one-third of international tolerance standards, and products must have a good surface finish. For small profile, the rolling speed of the rolling mill is from 12m/s to 20m/s, while for the bar rolling mill, the rolling speed has been increased to 36m/s.
2. Wire rod rolling mill
Wire rod rolling mills have rough rolling stands and intermediate stands similar to small profile rolling stands. Compared with small profile rolling mills for two-line rolling, these mills are generally designed to perform split rolling for simultaneous rolling of up to four lines. However, the current development trend is to use single-line high-speed rolling. Modern wire rod rolling mills generally have 8 to 10 non-twisting stands, which are arranged at an angle of 90° to each other in the finishing mill.
At present, the diameter of the rolls used in wire rod mills is limited to 200mm. The rolling speed can be as high as 140m/s.
3. Medium profile rolling mill and large profile rolling mill
After the rough rolling stand, the medium profile rolling mill has two sets of continuous stands. Continuous rolling mills can be arranged horizontally or vertically according to the pass design. For the section steel and channel steel with parallel edges, there is also a universal frame. When rolling other profiles, the universal frame can be replaced with the horizontal frame. The rolls of the horizontal frame have a deep hole pattern, but the universal frame does not.
The larger-diameter horizontal roll determines the shape of the section steel, and the smaller-diameter pair of vertical rolls are used to roll the edge. When the billet passes through the finishing rolls of the traditional stand and the universal stand, a good surface finish and dimensional tolerance can be obtained.
Roller parameter selection
-Rolled steel grade
The rolled steel type is the key factor for selecting the roll. Its deformation resistance varies with the chemical composition of the billet, which is mainly reflected in the size and change of the deformation load at each stage of rolling. The roller must be selected according to the determined strength and hardness.
-Rolling mill layout and pass design
The position of the stand on the production line and the design of the pass has a great influence on the choice of rolls. Depending on the position of the stand, the force mode and performance of the rolls can vary greatly. This is because the rolls applied to the rough rolling stand and the finish rolling stand have very different stress modes, resulting in expected changes in roll performance. In addition, the time interval between the passage of a billet and the next billet and the productivity of the rolling mill also has a great influence on the choice of rolls. It can be observed through experiments that roll bending and torsional stress combined with high rolling pressure are the factors that determine the selection of rolls for rough steel stands. However, in the finishing stand, hardness, wear-resistance and surface quality are the key factors for roll selection.
-Friction between roller and billet
Due to the difference between the circumferential speed of the roll and the billet speed, friction plays a very important role, especially at low speeds, such as blooming mills and roughing stands. Therefore, the relevant data creates conditions for the proper selection of rolls to suit a particular stand.
-Hot state
The thermal conditions of the rolls and rolled billets are also very important. The main reason is that the temperature of the roll is much lower than that of the rolled billet. Therefore, the roll is susceptible to high thermal shock in a short period of time, resulting in the formation of burnt cracks on the roll surface and further spread to form fatigue cracks. Therefore, the selection of rolls should take into account that roll cracks are minimally generated and propagated under rolling conditions.
-Roller cooling
The effectiveness of the roll is also related to the layout of the rolling mill coolant. The thermal conductivity of the roll material has a great influence on the cooling of the roll. The higher the thermal conductivity of the roll material, the higher the requirement for effective cooling, mainly to avoid the occurrence of cracking, resulting in a reduction in roll life.
Choose the roll according to the type of rolling mill
The selection of rolls is very skillful. The experience of the rolling mill operator plays a decisive role in the selection of rolls.
-Bar and small rolling mill
The requirements of this type of rolling mill for rolls are ① relatively good bending strength against impact; ② uniform hardness of the roll; ③ higher wear resistance; ④ better resistance to cracking.
If you are looking for rolls of rolling mills, please contact me.
Email: marketing2@hanrm.com; Whatsapp / Wechat: +8618392033938
More Articles You May Be Interested in:
3. How are the Rolls Classified by Material?
4. An Effective Way to Reduce Mill Roll Consumption
No comments:
Post a Comment