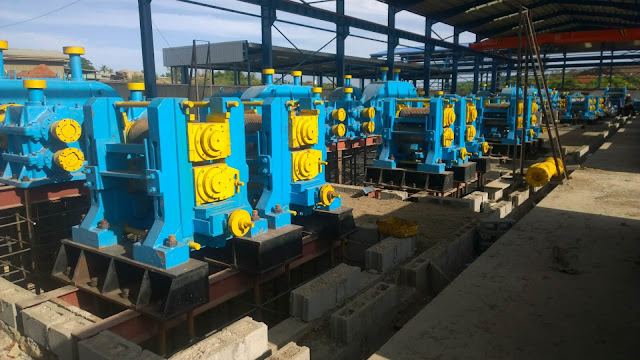
Some Data of the Rebar Rolling Mill Line:
Annual productivity: 1 million tons;
Billet specifications: 150mm×150mm×6000mm/9000mm/12000mm square steel billet;
Single billet weight: 1 ton (6m), 1.5 ton (9m), 2 ton (12m);
Finished product specifications: Φ12~Φ32mm small bar (round steel/rebar), of which Φ12~Φ22mm is slit rolling;
Finished steel types: ordinary carbon structural steel, high-quality carbon structural steel, low alloy steel, alloy structural steel;
Rolling speed: the maximum speed of single-line rolling is 18m/s;
The total installed capacity of the main rolling mill: 16.8MW.
TMT Rebar Rolling Mill Equipment Composition and Production Process:
The rebar rolling mill production line is mainly composed of loading equipment in front of the furnace, heating furnace, discharge equipment after the furnace, dephosphorization device, rough and intermediate finishing mills (18 rolling mills), rough, intermediate and finishing rolling flying shears, vertical loopers, water cooling devices, rack walking cooling bed, fixed-length cold shear, bar collection equipment, and packing device.
The production process flow mainly includes feeding, heating, dephosphorization, continuous rolling, flying shear, cooling, collection and packaging, etc.
The process flow chart is as follows:
The transmission of this hot strip production line can be divided into two parts. One part is the main driving part of the rolling mill for hot continuous rolling of steel billets, including the roughing mill, intermediate rolling mill and finishing mill; the other is the auxiliary driving part, including flying shears, roller drives, etc. The capacity of the main drive rolling mill motor is generally between 500kW and 1.5MW; the capacity of the auxiliary drive motor is generally below 300kW.
There are 18 rolling mills in the whole line, which are arranged in a full continuous horizontal and vertical alternate arrangement. The rolling mill motor adopts a 6-pole 690V AC asynchronous variable frequency motor with a power of 600kW~1.5MW. The total capacity of the rolling mill motor is 16.8MW. 1#~6# motors are rough rolling mills, 7#~12# motors are medium rolling mills, and 13#~18# motors are finishing mills. The 18 rolling mill motors are divided into 5 busbar groups according to the principle of power uniformity (as shown in the figure below), which are driven by their respective inverters.
Each busbar group is composed of four parts: power distribution cabinet, rectifier cabinet, inverter cabinet, and braking cabinet. They are connected in common busbar mode, and the rectification capacity of each busbar group is 4MW. The rolling pieces between the roughing and intermediate rolling mills are rolled with micro-tension and no torsion. The six rolling mills of the finishing mill are equipped with 5 vertical loops. The rolling pieces can be rolled without tension and torsion in the finishing mill.
Advantages of the Main Drive of the Hot Rebar Rolling Mill Line
1. With three voltage levels of 380V, 480V, and 690V, it can meet the voltage level requirements of AC main drive motors of mainstream rolling mills in the iron and steel industry;
2. Adopting optical fiber parallel technology, the power of a single system is 200kW~2MW, and it supports the parallel connection between systems, which fully meets the demand for large-capacity AC drives of the AC high-power main drive motor of the steel rolling production line in the steel industry;
3. Application of high-end vector variable frequency drive technology, its excellent performance, steady-state speed accuracy, low-frequency torque characteristics, torque response, speed response, speed range and other performance fully meet the process drive requirements of the AC main drive system of the rolling mill line in the steel industry;
4. The perfect DP non-standard function and the online FVC/SVC switching function help ensure the safety and reliability of the system and meet the continuous production requirements of steel enterprises under special working conditions;
5. Support 3 kinds of communication protocols, industrial Ethernet, PROFIBUS-DP and Modbus RTU, which is convenient for the field bus application in the steel industry;
6. With corresponding four-quadrant products, the application of the main drive of the rolling line can omit the brake cabinet, and at the same time can improve the energy utilization rate and increase the system power factor (up to 0.99 or more), which can reduce the capacity cost of the power supply transformer on the grid side. It also helps users save investment in reactive power compensation equipment; it also greatly reduces external harmonics, adhering to the concept of green environmental protection;
7. The seamless combination of fault memory and touch screen facilitates on-site equipment maintenance and diagnosis;
8. The same structure is modularized in parallel, which is convenient for installation, replacement and maintenance.
If you are interested in the hot rebar rolling mill line, please mail at marketing2@hanrm.com.
More Articles You May Be Interested:
Bar Rolling Process and Equipment Selection
The Advantages and Disadvantages of Hot Rolling
Hot Rolled Steel and Cold Rolled Steel
Hot Rolling Process VS Cold Rolling Process
What’s the difference between hot and cold rolling mills?
Features of Hot Rolling and Controlled Cooling
What is Metallurgical Equipment?
What is Laying Head?Technical Progress of High-speed Wire Rod Mills
Process Adjustment of Wire Rod Mill
ReplyDeleteReally helpful down to the ground, happy to read such a useful post. I got a lot of information through it and I will surely keep it in my mind. Keep sharing. If you are looking for some useful data and information regarding 410 Stainless Steel Sheet Suppliers then visit sanghvienterprise.